Products & Services
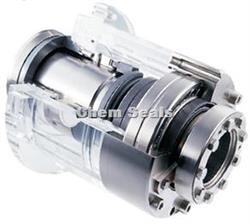
Agitator Seals
- DOuble Seal
- Unbalance seal
- Cartridge unit
- Easy installation
- Independent of direction of rotation
Application:
This seal is used in chemical industries , process industries on top entry agitators, dryers, mixers etc.
Operating Condition:
- Temperature : 35°C to 250°C
- Pressure : Upto 20 bar
- Speed : 5 m/s
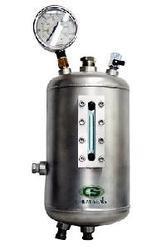
Thermosyphon System
Manufacturer & Exporter of API Systems & Thermosyphon System. Our product range also comprises of Industrial Seals, Dry Gas Seals.
With keen contentment towards excellence, we are readily immersed in presenting to our clients an enormous consignment of Thermosyphon System. This consignment is developed making usage of top-class inputs keeping in view the pre-defined industrial norms underneath professional supervision. Together with this, these systems are accessible with us in a consignment of standard and altered forms at market-leading rates.
Features:
- Precise design
- Smooth finish
- Longer life
Other Details:
- From Mumbai, we are the Thermosyphon Systems Manufacturer, Supplier and Exporter, worthy a mention
- Our adept team deploys high-grade materials and ultramodern technology in order to design the API Systems that meet the highest terms of quality, durability and performance
- To cater the variegated needs of the global clients, we make available the Thermosyphon Systems in tailored specifications. Plus, we never daunt from executing timely deliveries.
Specifications:
- Capacity: 8, 10, 15, 23 litres
- Optional cooling coil available
- Construction- aisi 316 / 304 / carbon steel
- Suitable for Pressurized & Unpressurized systems
Optional Attachments:
- Air Vent
- Flow Indicator
- Pipes
- Level Switch
- Bleed Valve
- Regulator
- Pressure Gauge
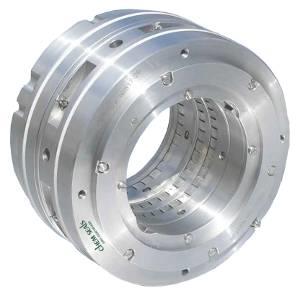
Dry Gas Seals
Depending on the diameter of the rotor, work pressure, temperature of the packed gas and the frequency of the rotor speed, the leakage through every DGS can be from 0,01 to 0, 15 m3/min.
Although the value is equivalent to the intensity of the leakage through the oil seals, need to consider that at installed oil seals an additional gas leakage occurs from degassing of circulating oil. Usually gas from oil is released into the atmosphere, doubling the total volume of leakage through the seal up to 6 m3/min.
Reduction of the energy consumption
At dry gas seals installation the pumping systems for oil circulating are excluded, consuming the electricity, and hence the energy is saved. The power consumption of the oil seals is from 50 to 100 kW, while the losses do not exceed 5 kW in DGS.
Exclusion of oil leakages
Replacement of oil seals into dry eliminates seal oil leakage in the flow part of the compressor and that is why there is no gas pollution and the pipeline's technical characteristics deterioration.
Less volume of maintenance
Dry gas seal systems have low time spending on maintenance, because they do not have assemblies, which are necessary at the oil circulation (pumps, control valves, relief valves) in comparison to oil seal systems.
Simplification of the software system
DGS systems do not require the installation of sophisticated components, which provide oil circulation, and devices for its processing and cleaning.
Higher reliability
Most of idles of compressor with oil seals caused by problems in the sealing system.
Short term of payback
The term of payback of DGS systems in average is from 12 to 16 months. If there is a trend of the prices increase on energy sources the term of payback will reduce.